Battery Pack and Charger Selection for Optimum Performance
Selection and operation of a battery charger
Optimum performance of batteries should be an important consideration in the design of any battery powered product, and while it is often the case that larger or ‘better’ batteries are adopted to meet the technical requirements, less thought is typically given to the ongoing management of batteries in the field.
In this article we will consider some of the most relevant factors impacting on whether the product lasts for years, or ends up in landfill (or hopefully recycling) within 24 months of manufacture.
For all the commonly used chemistries there are a large selection of manufacturers offering a wide range of cells at, often, significantly differing price points to meet a range of different product specifications. While it is well understood that an industrial cell from a branded manufacturer will have better overall performance that a lower cost product designed for the consumer market, there are a number of factors external to the cell construction and quality that can have an equally important effect upon cell life...
For example: the match between the battery pack and the charger.
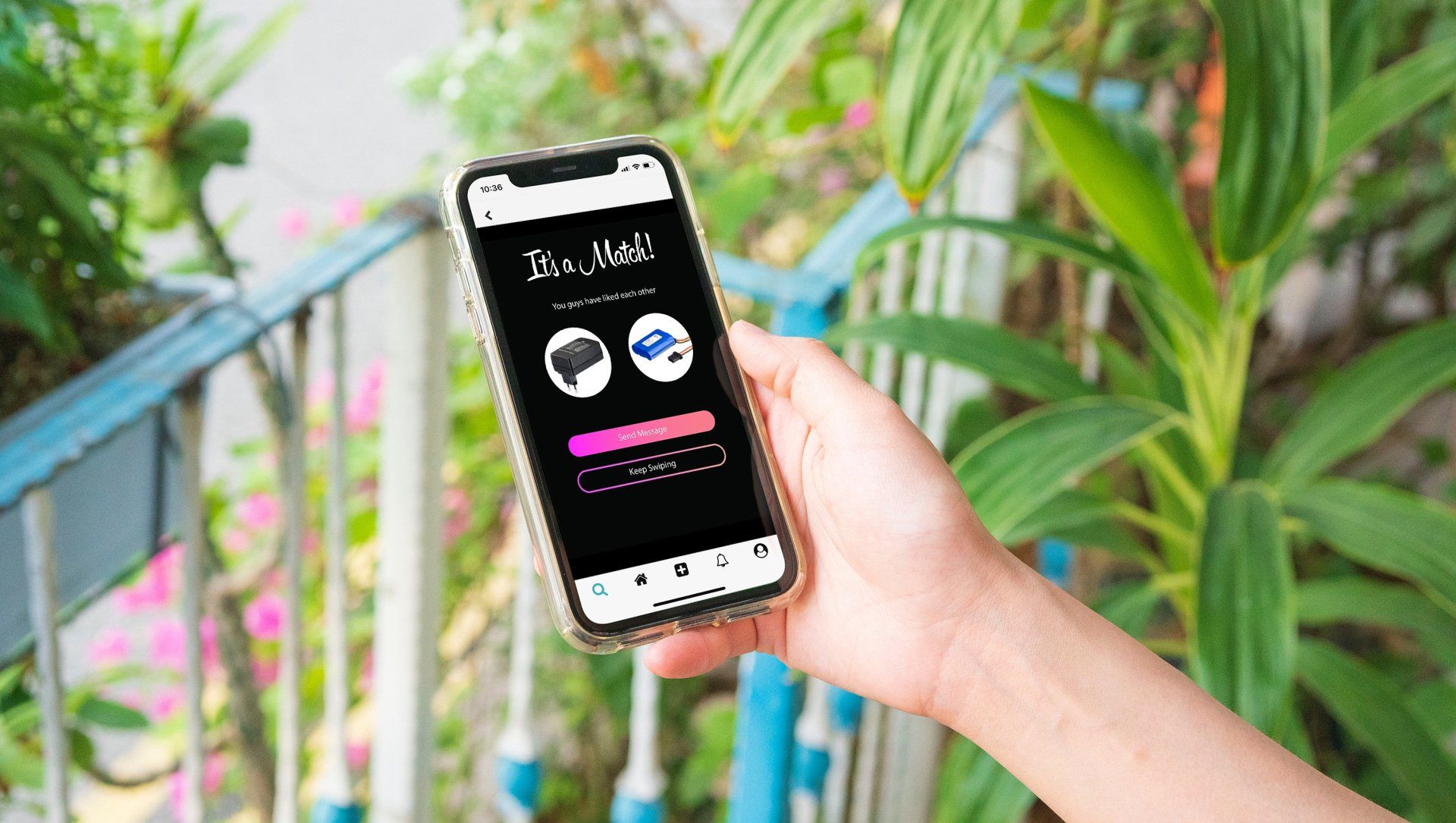
Charger and Battery Matching Up Visual - Created by Haredata Electronics
Lead Acid (Pb) Battery Packs
For Lead acid batteries the impact is less significant, Lead Acid batteries are more tolerant of abuse such as overcharging, and are more able to cope with significant changes in the required load without a massive impact on cycle life (as long as the correct standard of battery has been selected) However, it is still possible to overcharge a sealed Lead Acid Battery, and because the resultant excess gas cannot escape this can lead to batteries ‘bulging’ in a most alarming way!
Because of their high weight and low cost, Lead Acid batteries are still a good option for heavy industrial applications when charging time is less of a factor, and ‘taper’ chargers at a low current wrt to capacity are often adopted. These offer the advantage of steadily bringing the cell voltage up to 2V but can remain connected indefinitely as the current is typically less than 0.1C (where C is the battery capacity) and so the battery can safely lose the excess energy once fully charged (as heat). The downsides are slower charging and an inefficient use of power.
Nickel–metal Hydride (NiMH) & Lithium Ion (Li-Ion) Battery Packs
Of course for most battery powered equipment the desire is to have a small, lightweight battery than can be charged very quickly and then power the product for hours and hours. NimH batteries do have many advantages over Lead Acid, but the main chemistry adopted for such products is Li-Ion. The 2 chemistries share several properties in terms of their charging and discharging profile, so we’ll consider them together below...
Typically these batteries can be designed to offer high discharge current, large initial capacity, or long cycle life (or a degree of compromise between all 3) Therefore quantifying exactly how the product is expected to be used helps inform the decision on cell selection and in turn a suitable charger. Battery cycle life is impacted by charge and discharge rates, so for a low discharge application the biggest determinant of the battery life is the charge rate and control of charge termination to prevent overcharge. If the rate of discharge is high, then a slow rate of charge to look after the batteries will have proportionally less effect, as the cells have already been thoroughly worked over.
In either case overcharging must be avoided at all costs, a small degree of overcharging will gently ‘cook’ the batteries (NimH and Li-Ion are much less happy being heated up than Lead Acid) and significant overcharge can lead to structural failure of the cell (explosively in the case of Li-Ion) The desired objective therefore is a charger that will charge the batteries quickly (but not too quickly) make sure they are fully charged (but not overcharged) and ‘manage’ the cells during the process – i.e. is able to detect any issues and modify the charging profile according to the state of the battery.
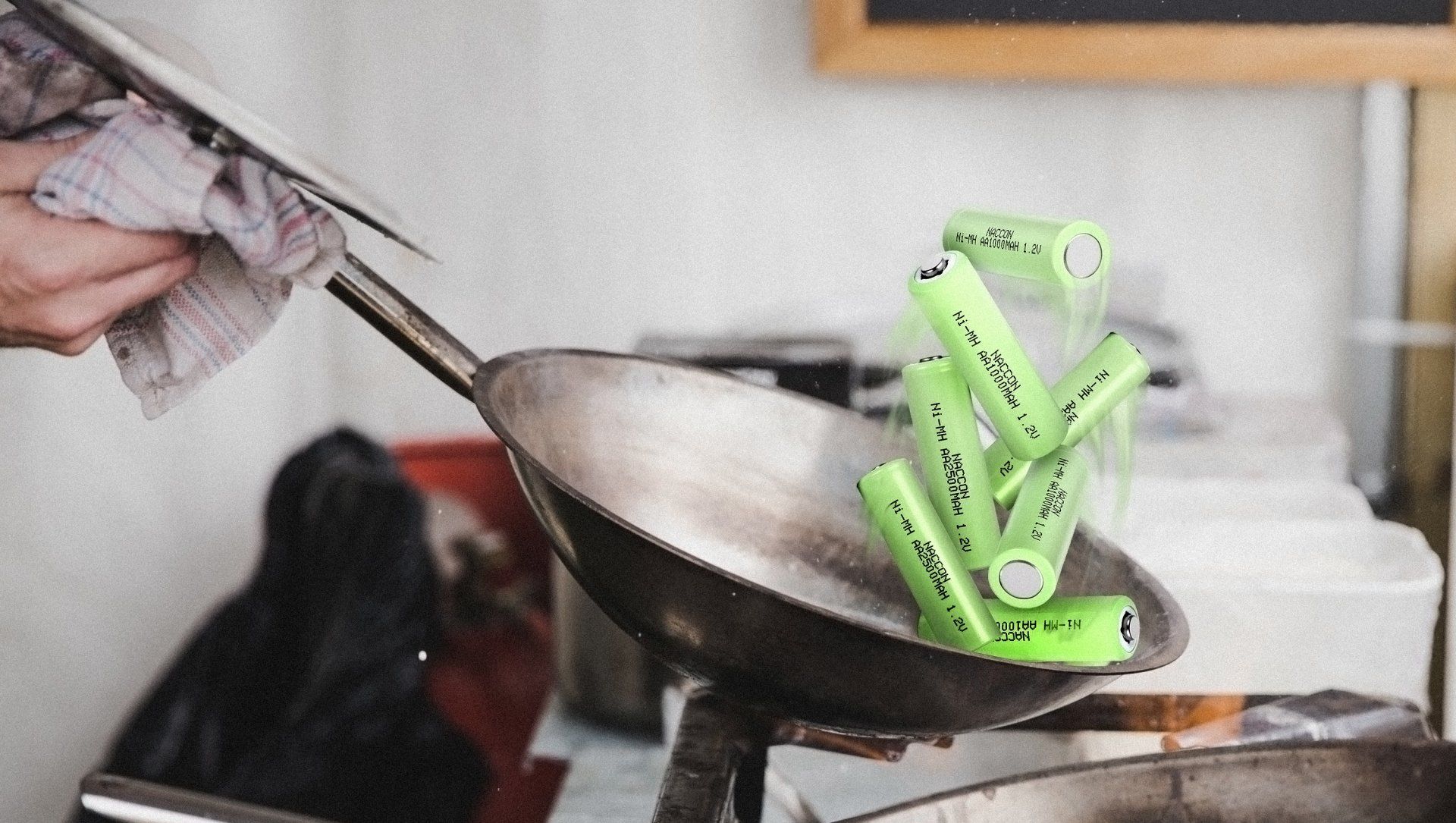
Cooking NiMH Batteries Visual - Created by Haredata Electronics
NimH and Li-Ion Battery Chargers | Voltage Sensing & Temperature Sensing
The whole range of NimH and Li-Ion chargers manufactured by FRIWO are able to detect the number of cells in the battery pack once connected, and supply the correct charging voltage/current accordingly. If the voltage of a battery is not within a safe ‘charge window’ – for example because it has been left for an extended period and the cell voltage has dropped too low, then a lower pre-charge current is applied to gently ‘wake’ the battery up before the full charge current is delivered (only as and when the voltage has risen to the pre-determined level).
Due to this voltage sensing technology the charger is also able to recognise the characteristic ‘dip’ that occurs as the cells approach full charge, and is then able to reduce the current to a float charge level to top up the last few percent of capacity without risking overcharge. All of these stages are communicated via the LEDs on the top of the battery charger, so the end user can understand the status of the battery at glance.
Voltage sensing can be operated via any standard 2 pole connector, and requires no additional componentry to be added to the battery pack. Another method that can be operated instead or alongside voltage detection is temperature sensing. In order for the FRIWO battery charger to be able to read the temperature of the battery pack a temperature variable resistor (thermistor) needs to be added ideally somewhere near the middle of the pack. The charger then connects via a 3 wire connection (meaning standard jack plugs cannot support this technology).
There are 2 main advantages of temperature sensing – because the charger can tell how hot the pack is, it can decline to charge it if it would result in damage to the battery – this typically occurs if a battery pack has been left in a very high or low ambient temperature prior to charge (e-bike batteries left in a garage in the middle of winter spring to mind) or if it has just been discharged at a high rate and is then plugged straight into the charger (a typical power tool situation) The charger will indicate a temperature warning, and wait for the pack to cool down/warm up before commencing the main charge.
As a battery pack ages the individual cells in the pack can degrade at different rates (this is partly dependent upon the level of cell balancing within the battery management system, if fitted) This can result in the voltage dip becoming less of a ‘canyon’ and more of a ‘gentle valley’ making it more difficult for the voltage sensing to detect. If the charger is able to monitor the temperature of the pack then it can very accurately detect the level of charge, as once the pack is full the excess energy can only convert into heat. This means that Delta-T is considered a more robust method of charge termination, and allows higher charge currents, as the possibility of overcharging is removed.
Need a charger?
Click the button related to your battery chemistry to view the range
Summary
Because FRIWO have been designing and manufacturing bespoke battery chargers for every commercially used battery chemistry for over 40 years we offer products featuring all the technologies featured in this blog, and would be delighted to help you select a charger that will keep your batteries in top working condition for as long as physically possible (until a battery is invented that lasts forever)
CONTACT US
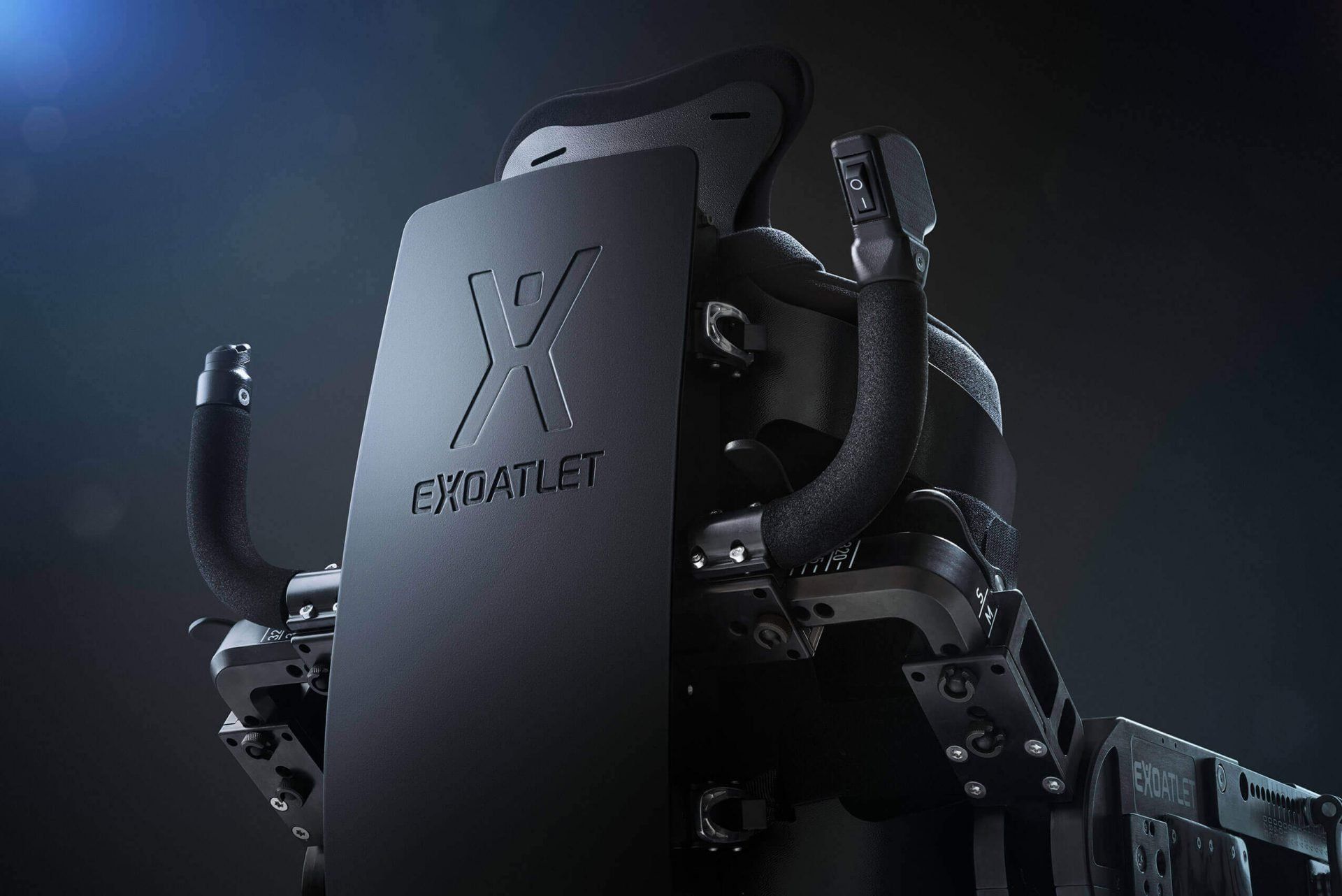
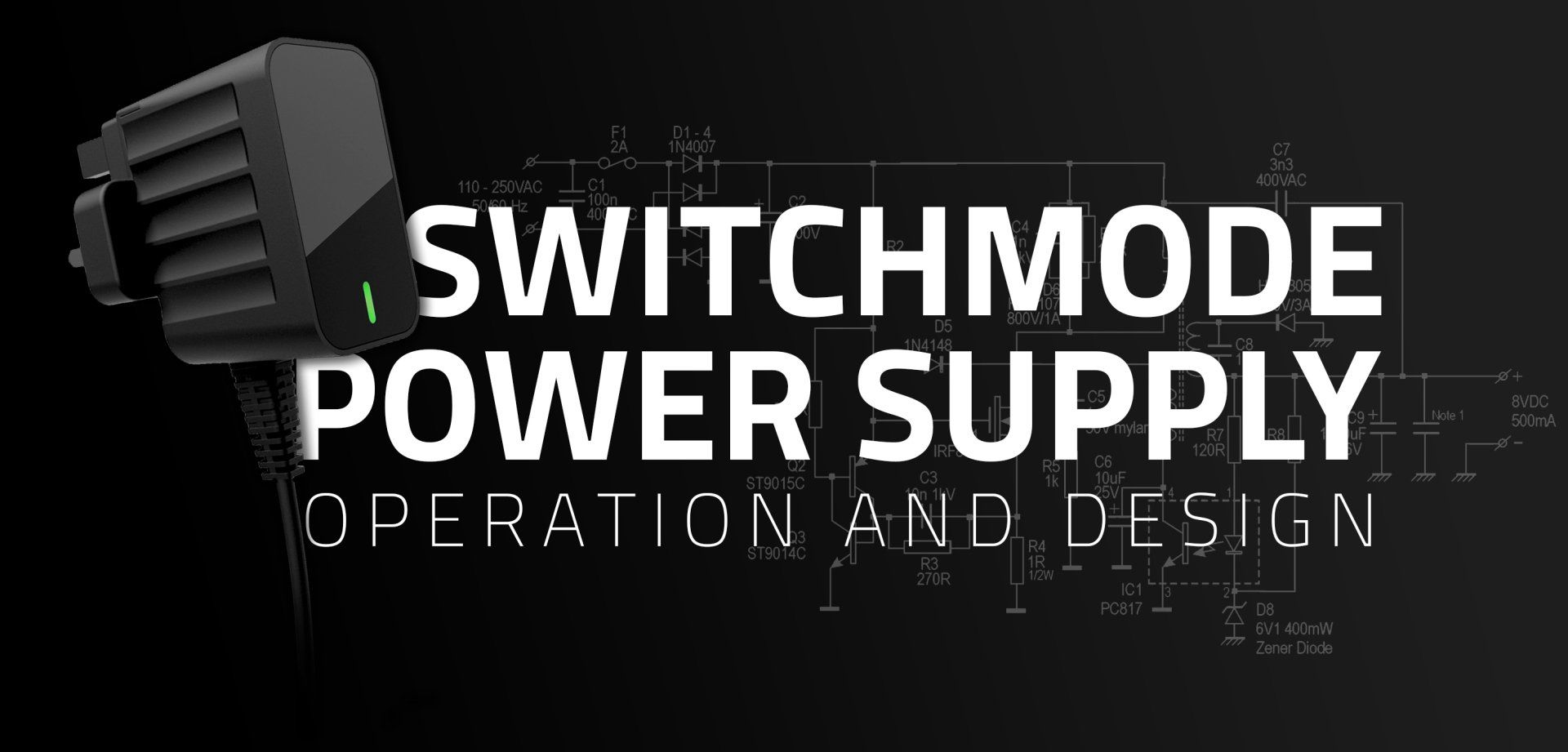
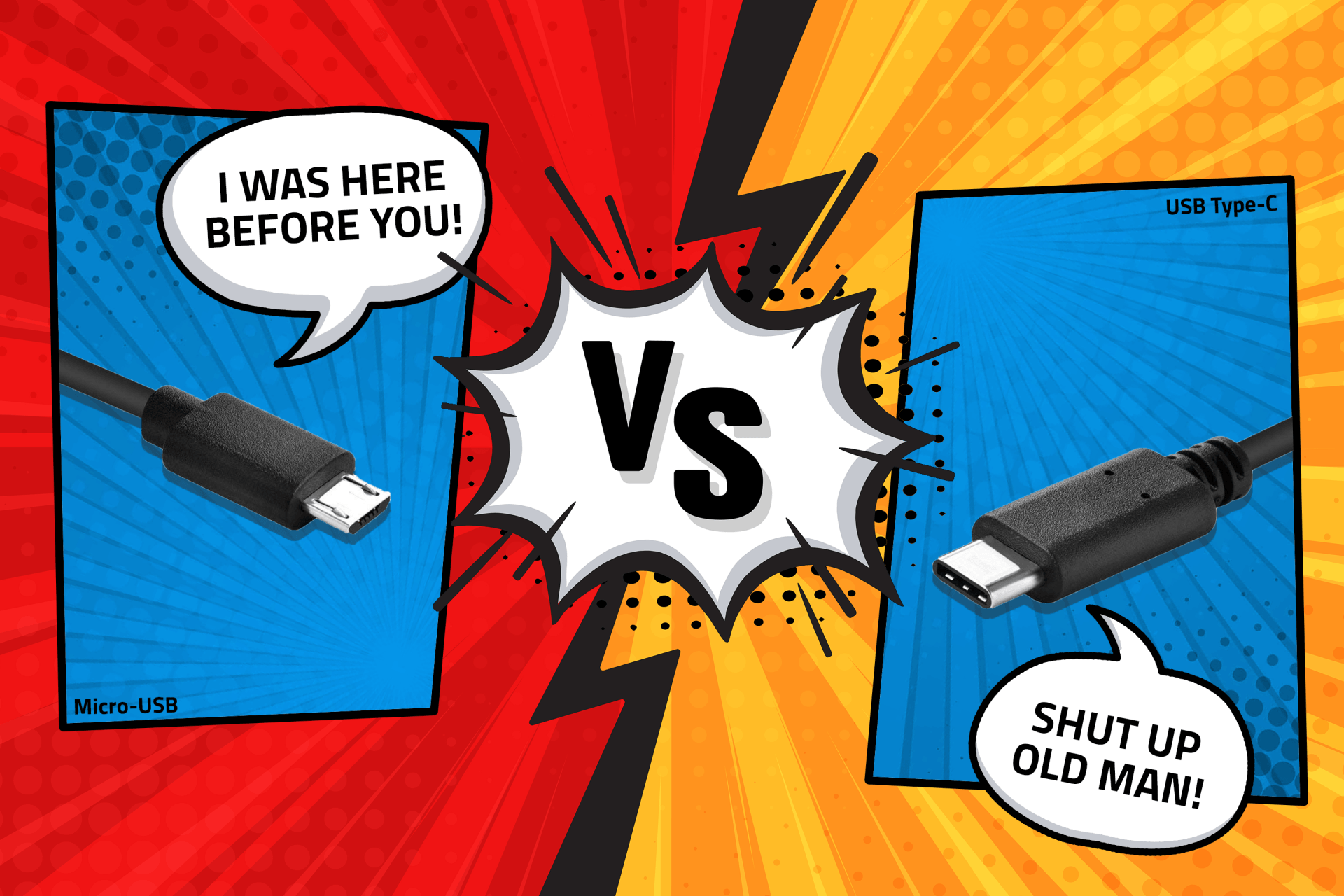
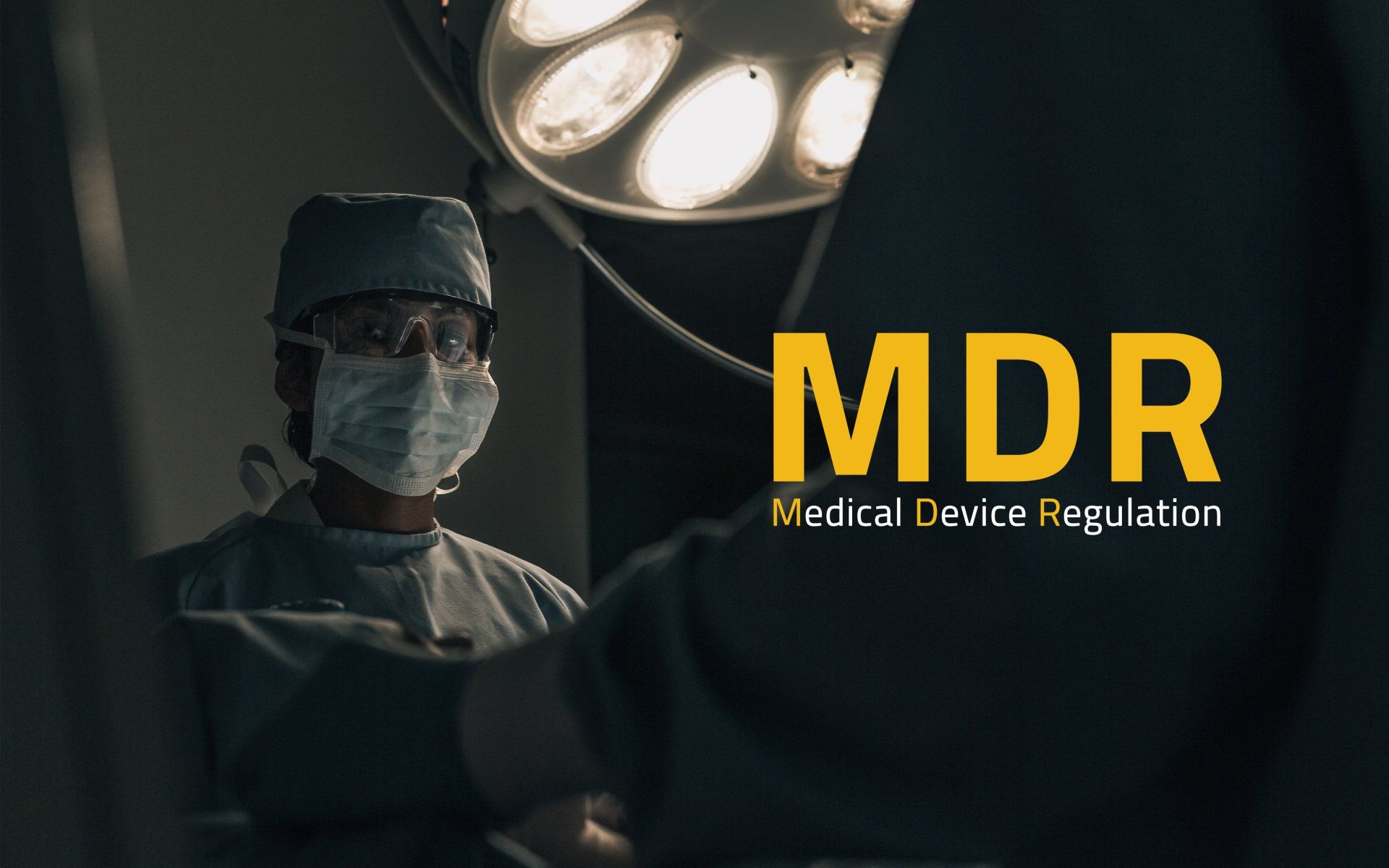